Rubber and Elastomers
Molecular Rebar®, MR, increases wear resistance to extend the lifetime of rubber goods and tires. MR’s optimal aspect ratio and excellent dispersion improve crack propagation resistance, often doubling lifetime in macro-abrasive conditions.
Lowered cost of component ownership ($/hr)
- Less downtime & higher throughput
- Longer lifetime than cost increase = lower operating cost
Easy fit with existing manufacturing
- MR in oil: MRO
- Universal uses, no change in compounding process
- 50:50 or 60:40 ratio of MR to oil available
- MR in oil: MRO
Improved performance properties
- Lighter-weight, more fuel efficient, and tougher rubber compounds for tires
By leveraging the improved resistance to wear, tire treads can be optimized through engineering design changes. Allow Molecular Rebar® to be a new ingredient in your recipe cabinet.
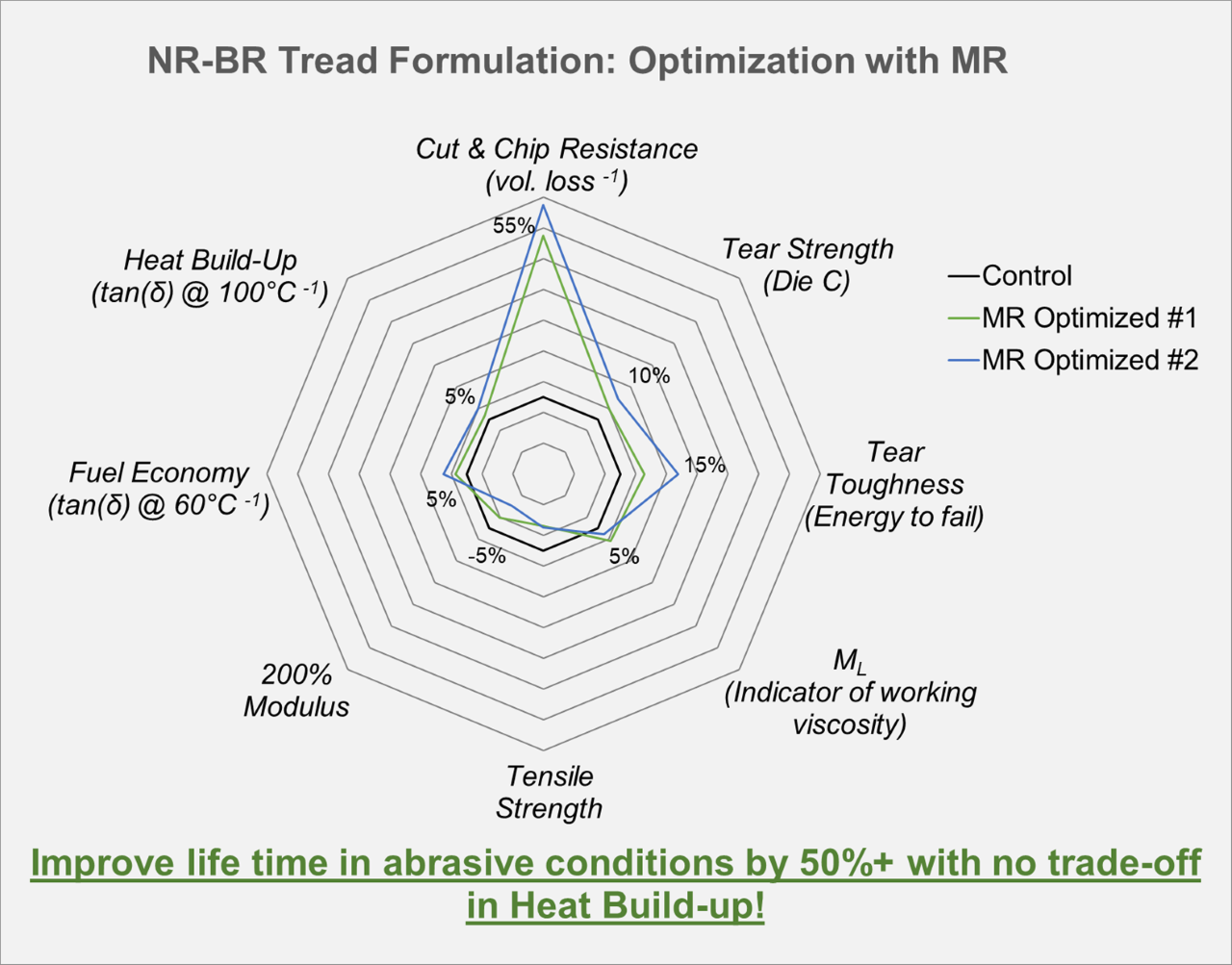
Performance & Products
30%+ BF Goodrich Cut & Chip resistance
15%+ tear resistance
No increase in rolling resistance
MRO Gen I
- Use in specialty polymers: NBR/HNBR or FKM/FFKM
- Delivered with TOTM, DOP, or DBS oil
- DBEEA, DOA oil offering in the future
MRO Gen II
- For use as an additive for toughness properties in parts & tires
- Use in NR/SBR/PBR
- Offered as a 50:50 ratio of MR:Oil in naphthenic, RAE, or soybean oil
- TDAE, RAE oil offering in the future
MRO Gen III
- For use as a carbon black or reinforcing filler replacement, lowering density and improving performance
- Use in NR/SBR/PBR
- Offered as a 60:40 ratio of MR:Oil in naphthenic, RAE, or soybean oil
Performance & Products
30%+ BF Goodrich Cut & Chip resistance
15%+ tear resistance
No increase in rolling resistance
Molecular Rebar in Naphthenic or TDAE oil (MRO)
- Use in NR/SBR/PBR
Molecular Rebar in TOTM- MR 1020 DLC
- Use in NBR/HNBR
Molecular Rebar in FKM/FFKM
- Produced with customer elastomer
- Developmental product
Coatings
Molecular Rebar® makes coatings more rugged and corrosion resistant. Our functionalized MR binds to epoxy or urethanes for improved durability. MR electrically connects corrosion inhibitors and reduces the required zinc concentration in zinc-rich primers. Because MR is discrete and individual, coatings are defect-free.
Reduced cost of ownership
- Longer corrosion protection lifetimes
- Increased damage tolerance
Reduced coating cost
- Thinner coatings
- Reduced corrosion inhibitors
Increase market share for coating manufacturers
- Differentiated coatings
- Replace 90% Zinc-rich primers with 80% Zinc or less
Coatings
Molecular Rebar® makes coatings more rugged and corrosion resistant. Our functionalized MR binds to epoxy or urethanes for improved durability. MR electrically connects corrosion inhibitors and reduces the required zinc concentration in zinc-rich primers. Because MR is discrete and individual, coatings are defect-free.
Reduced cost of ownership
- Longer corrosion protection lifetimes
- Increased damage tolerance
Reduced coating cost
- Thinner coatings
- Reduced corrosion inhibitors
Increase market share for coating manufacturers
- Differentiated coatings
- Replace 90% Zinc-rich primers with 80% Zinc or less – epoxy producers increase sales
Longer Lifetime
Performance & Products
Available Products
-
2% Molecular Rebar® in bisphenol A/epichlorohydrin liquid epoxy resin
Higher Impact Strength
Longer Lifetime
Higher Impact Strength
Performance & Products
Available Products
-
2% Molecular Rebar® in bisphenol A/epichlorohydrin liquid epoxy resin
Conductive Inks
MOLECULAR REBAR® is uniquely tailored to take your conducting ink formulations to the next level of rugged performance for rapid growth into flexible/durable applications with economics that make sense.
Improved print quality & performance
- Improved conductivity at lower thickness
- Improved performance consistency- less rejects
- Improved conductivity during stretching
- Improved print resolution
Easy fit with printing processes
- Nano- to Micro-particle inks
- Digital to screen printing
Conductive Inks
MOLECULAR REBAR® is uniquely tailored to take your conducting ink formulations to the next level of rugged performance for rapid growth into flexible/durable applications with economics that make sense.
Improved print quality & performance
- Improved conductivity at lower thickness
- Improved performance consistency- less rejects
- Improved conductivity during stretching
- Improved print resolution
Easy fit with printing processes
- Nano- to Micro-particle inks
- Digital to screen printing
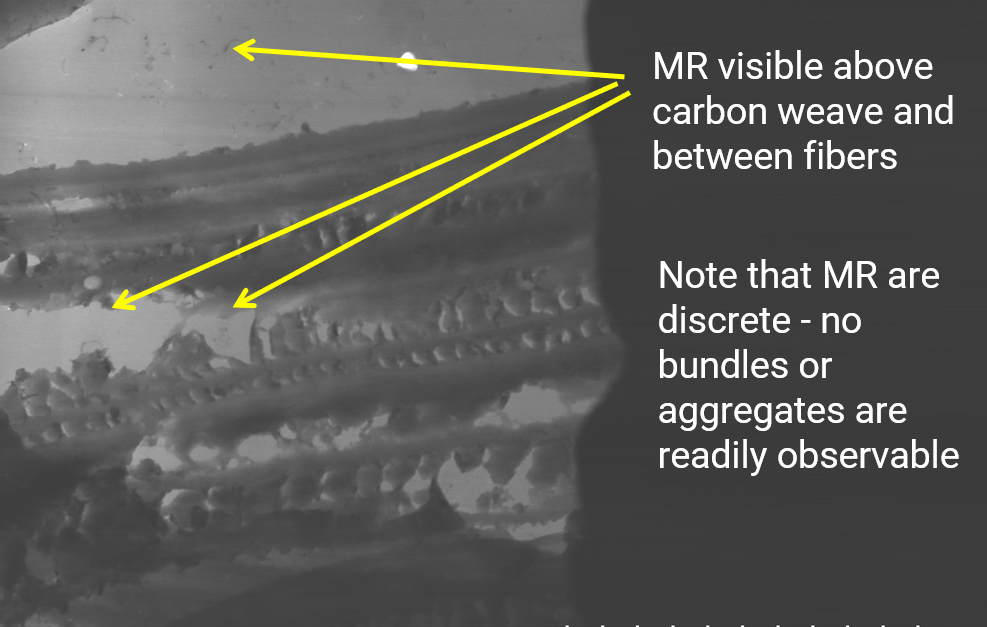
Performance & Products
Enhanced
- Toughness and durability in epoxies
- Interlaminar shear stress between fibers
Fit easily with existing composites manufacture.
- Does not change curing conditions
- Masterbatch designed for facile dilution.
- Little flow viscosity changes
- Enhanced microwave or near infra red curing kinetics
Performance & Products
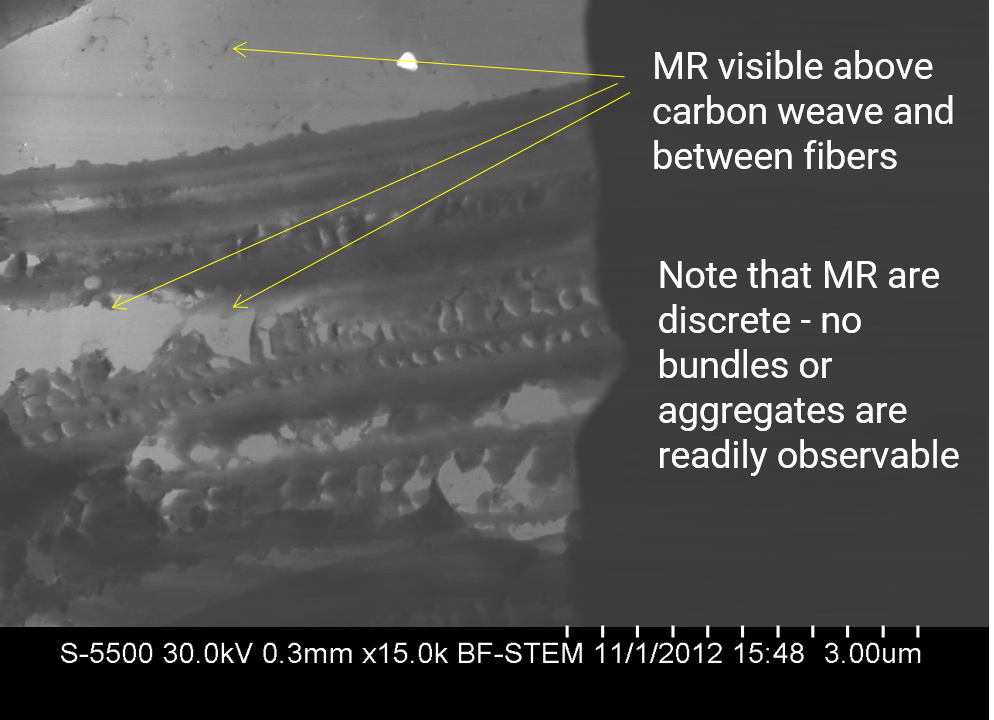
Enhanced
- Toughness and durability in epoxies
- Interlaminar shear stress between fibers
Fit easily with existing composites manufacture.
- Does not change curing conditions
- Masterbatch designed for facile dilution.
- Little flow viscosity changes
- Enhanced microwave or near infra red curing kinetics